Tin Plating
Tin plating for bakeware and electronics applications. For manufacturers or for users requiring refurbishment
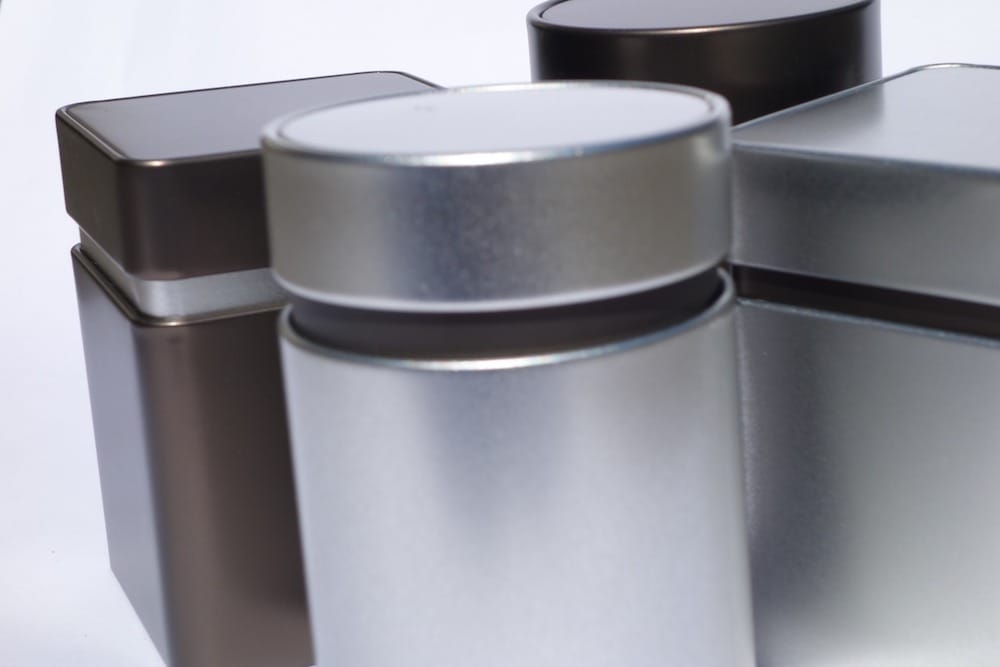
Description
Tin plating is an electrolytic process. A dull (or stannate) tin finish is most often used by A Class. Tin plating is primarily for “functional” purposes such as providing a level of protection or corrosion resistance to a range of items. Tin is commonly applied over a preliminary coating of copper. A Class offers “Barrel” plating for cost effective treatment of very small connectors or components as well as bath plating for larger components.
Benefits of tin plating
Stannate Tin plating is a lower cost alternative than some protective coatings. Tin also has a good level of conductivity enhancement properties (as opposed to silver which has higher conductivity) which may be of benefit to manufacturers seeking to enhance this property somewhat without adding too much to the price. Tin has good solderability and is therefore a coating of choice where later soldering of components is required.
Colour & Aesthetics of tin plating
Tin plating has a ‘whitish grey’ hue and is usually applied without the layer of bright nickel used in decorative coatings − as such tin has a dull, or matt appearance.
Applications for tin plating
Examples include: Low-tech electrical or electronic components such as electronic connectors or bus bars; commercial cooking equipment; parts requiring soldering; other.
Substrates suited to this coating
Tin can be plated over most metal substrates but commonly is used on lower value substrates such as mild steel or copper alloys.
Design Cautions – before tin plating
As this is an electrolytic process it is necessary to use jigging, racking or wiring to provide for electrical current conductivity. Some shapes lend themselves more easily to this than others. In some cases the addition of a sprue or hole is necessary. Please consult your plating adviser prior to finalising design if you intend to use this finishing process.
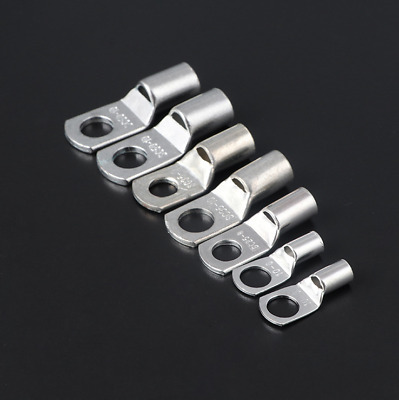
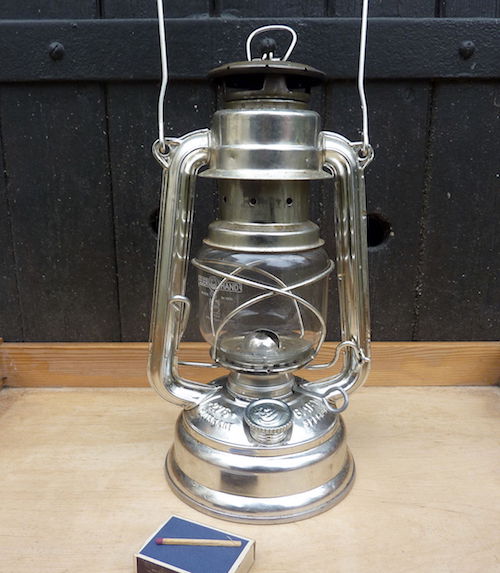
ONLINE QUOTE
We are no longer providing estimates for Metal Restoration work. If you are a manufacturer requiring finishing for your ready to plate commercial products or components click on "Quote for new parts finishing" and you will be directed to the business we sold our commercial plating operations to. Note - they DO NOT offer metal restoration or refurbishment services.